How Does Thermal Oxidizer Sizing Impact Melt System Capacity?
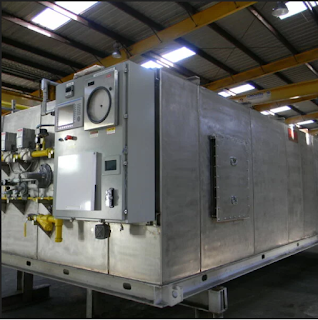
Melt Furnace Capacities Historically, parts producers have focused on dryer and melt furnace capacities as the rate limiting factor when sizing their system. The practical reality, when sizing a system, is that vent stream emissions may be the real rate limiting factor controlling your overall recovery system’s capacity. One of the first steps when evaluating a potential metals recovery project should be to understand the expected fluids and contaminants in the feed-stock. Given these input conditions, a concurrent analysis of the thermal processing load for the drying system and the expected constituents in the vent stream can be conducted. From these calculations, an estimate of the projected emissions loading from the operation can be determined. Based on the findings from the above emissions calculations, the appropriate air pollution control system can be sized. While thermal oxidation of these vents streams is a proven solution to mitigate the VOC emissions from thes